[ad_1]
The electric vehicle (EV) revolution gains more momentum every day, driving change to automotive manufacturing in unprecedented ways. With rapidly growing demand comes the need to rapidly scale assembly operations — and that can create significant challenges.
Vehicle manufacturers constantly seek new, more productive automation technologies to boost their quality and productivity. Along with many common assembly workflows, they face new challenges associated with scaling up battery pack and e-axle production. They need automation solutions to help integrate electric battery and powertrain production seamlessly into overall assembly processes.
Bosch Rexroth has an industry-leading portfolio of automation technology to satisfy these needs, with decades of experience providing manufacturing and automation solutions to leading automotive OEMs, as well as Tier 1 and Tier 2 suppliers.
Broad range of assembly challenges
Electric vehicles have replaced engines, gas tanks and transmissions with electric motors, regenerative braking technology and advanced battery packs. Assembling these new components presents unique challenges; at the same time, there are assembly processes common to both EV and internal combustion (IC) vehicle assembly lines.
For example, EVs have body parts that are welded using high-speed six-axis robots with advanced welding controls. Extremely precise control of weld quality is critical to the long-term performance of the vehicle; poor welds can lead to separation and vibration in body parts over time.
To solve these complex welding challenges with maximum speed and absolute quality control, Bosch Rexroth has introduced the PRC7000 welding controller platform.
The PRC7000 expands the number of heat blocks available, so plant operations can customize welding to specific throughput and material characteristics — a major advantage over older-generation systems. Also, it can store up to 10,000 welding programs that can be easily built via a drag-and-drop interface to incorporate more sophisticated welding sequences.
Improving manual assembly
Even though EV plants are highly automated, they also use the latest manual assembly methods to install a wide range of components and systems. Assemblers install headlights, windshields, retractable sunroofs, seats and door and window controls, often also connecting them to the vehicle’s control module. Exact precision in this process is critical to deliver vehicles that operate as flawlessly as possible.
Bosch Rexroth offers an advanced portfolio of intelligent tightening tools to provide the productivity and quality control needed for these manual processes. They provide the precise, repeatable performance crucial to high-volume assembly lines. The portfolio includes the EXACT ION series of cordless screwdrivers, offering industry-leading accuracy, durability and energy efficiency, as well as ergonomic design and lower weight to enhance worker comfort.
Wider use of these kinds of i4.0-ready tools helps assembly lines increase throughput and operate with greater flexibility as different vehicle models move through the line, while at the same time generating critical data that plant operators can use to improve training, adjust workflows and apply lean manufacturing principles.
Multiple technologies to boost battery pack production
There are four major steps in battery pack production common to most operations: electrode production, cell assembly, module assembly and pack construction, which also typically includes end-of-line battery testing.

Each stage uses a complex array of automation technologies to go from raw materials to completed packs. Given the critical role of the battery in the long-term performance and value of EVs, battery production requires high throughput rates combined with extremely tight assembly tolerances and quality control systems.
In electrode production, raw materials move through multiple automated processing steps. Maximizing control over these processes requires technologies that ensure cells are created with desired electrochemical properties, lifecycle and energy density.
Bosch Rexroth’s ctrlX AUTOMATION platform features advanced controller and drive systems designed precisely for these high-throughput production processes. The ctrlX CORE controller provides advanced closed-loop sag and loop control to eliminate breakage and minimize waste. It also supports high-speed multi-axis synchronization for web speed and position alignment.
In cell production, individual batteries — cylindrical, pouch or other format — are combined into cells. Many manufacturers are working to optimize the stacking process in this step because streamlining stacking can improve the throughput of the entire line.
High-speed robotic handling systems, either delta robots or linear robots, are essential tools in this stacking process. The Smart Function Kit for Handling is a highly efficient linear robot option well-suited to this process step. It is truly plug-and-produce: modern online tools support quick and intuitive component selection and configuration, and the pre-installed software allows for easier commissioning, supporting faster production start and helping speed to market.
Modular movement and transport solutions
Going from raw materials to a tested and installed battery pack presents a major automation transport challenge. With each assembly step, weight and component size increases, so a range of material transport conveyors and other systems is necessary.
From transfer systems for rapidly moving products weighing a few grams to linear motor-driven systems that can precisely transport up to over 400 kg, state-of-the-art conveyors and linear motor transport systems maximize efficient use of factory floor space and enable smoothly flowing, intelligently connected production.
VarioFlow plus plastic chain conveyors are proven systems that rapidly move cell assemblies horizontally, vertically, around obstacles or integrated with other process flows. These also support workpiece pallets to convey cell components where positioning or higher stopping precision is needed.
Further down the line, Bosch Rexroth offers the linear motor-based Flexible Transport System (FTS). It supports pallet-based transport and allows for individual carrier control for more complex movement at faster throughput rates. Combined with our intralogistics autonomous mobile robots (AMRs), Bosch Rexroth is uniquely equipped to address virtually every battery production transport challenge.
Successful assembly lines design conveyor and material transport solutions early in the development process, not as a final step once all the production machines and cells have been defined. This helps ensure productive movement of products and materials through every process step and prevents building in non-value-added transport time. Bosch Rexroth has deep experience helping select and connect different transport systems so the right material flow is established — and can be easily modified as production requirements evolve.
Automation insight to improve EV assembly productivity
As EV manufacturers are under pressure to expand production, they run risks by simply throwing technology at their throughput challenges, rather than considering how well their technology and component choices work together. All this assembly technology should be engineered and harmonized to maximize throughput without sacrificing the quality of the end product.
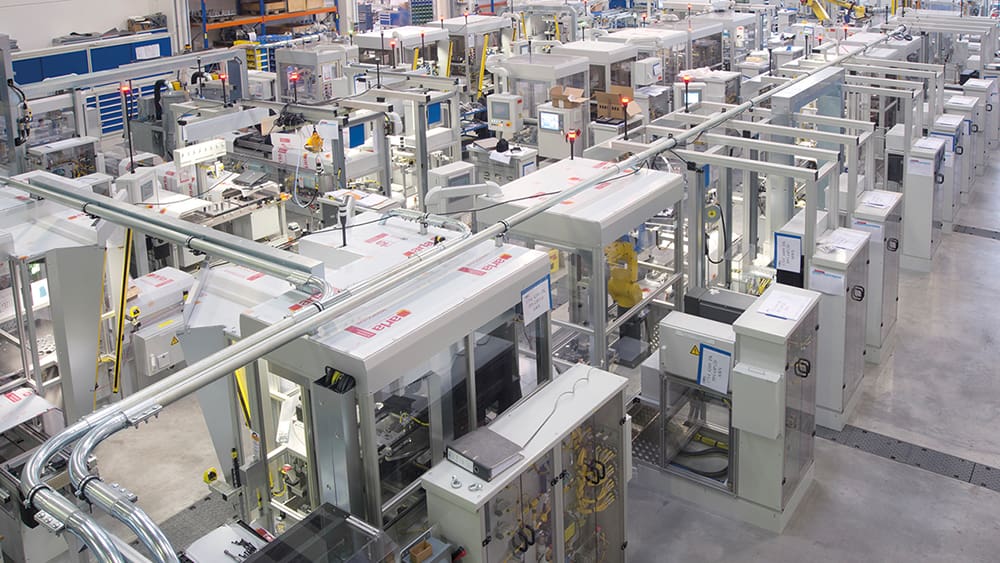
Bosch Rexroth can leverage its industry-leading automation portfolio and deep automotive manufacturing expertise to help prevent this risk. We have productive partnerships with leading factory automation specialists. They work with our experienced automation technology experts, following a unique, concurrent engineering approach.
Using this approach, we partner to conduct system design, programming and component acquisition and integration in tight, overlapping time frames to deploy complete automation solutions more rapidly.
Our solutions encompass virtually every major step in EV manufacturing, with specialized expertise in EV battery pack production. Our concurrent engineering methodology succeeds because we back it, and all our complete automation solutions, with global engineering, service and technical support resources.
[ad_2]
Source link