[ad_1]
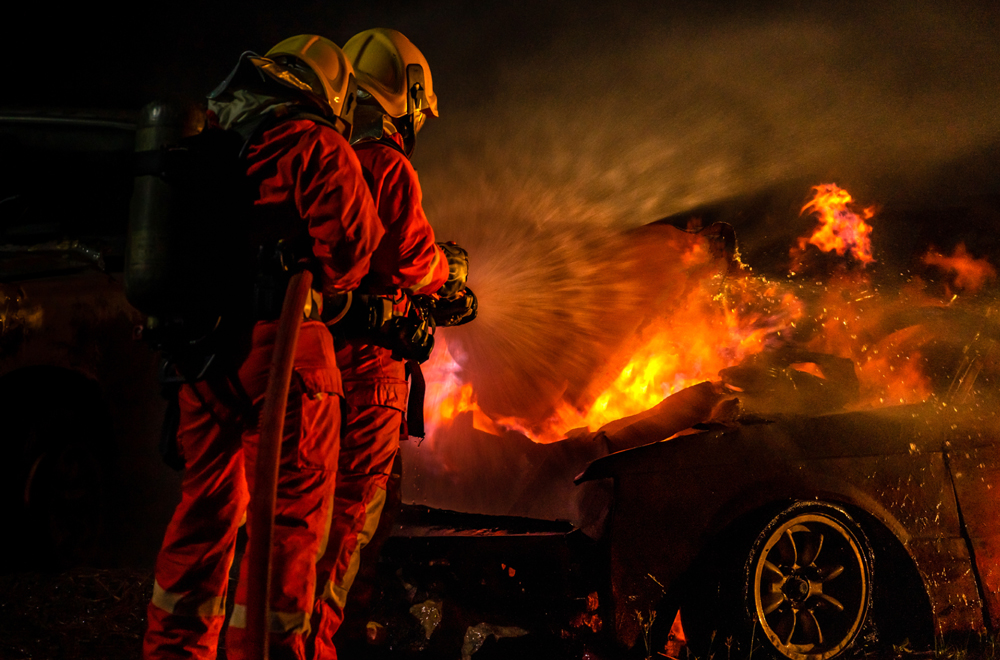
Battery management systems (BMS)—the electronic brains that monitors and maintains lithium ion battery packs—are essential for the safe and efficient operation of the batteries powering a variety of applications, including electric vehicles. The growth of electric vehicle technology is driven by the desire for reduced emissions, quieter and less expensive vehicles, advanced driver assistance systems and improved comfort and convenience. Full acceptance of electric vehicles is dependent on their ability to reliably travel long distances and reduce “range anxiety,” which can be achieved in part by a battery management system that allows the vehicle to operate more efficiently.
Battery management systems provide the vehicle with real-time decision-making, diagnostics, and anticipatory control of every watt of power demand throughout the vehicle. Data acquisition occurs via sensors that monitor electrical, safety, and thermal subsystems and is transferred through communication network cables to the BMS interface, which in turn provides information on vehicle performance and range to the operator.
Battery packs utilize three main wiring architectures. The first utilizes a flat, flexible printed circuit with connectors and a centralized module controller. The second is a centralized module controller that uses discrete wires instead of flex circuits. The third is a discrete wire with a decentralized module controller on each battery cell, which is individually controlled and linked together with cable. Flexible printed circuits are less complex, while discrete wires with centralized and decentralized module controllers require more complex wiring solutions. Wire-to-board and FPC-to-board connectors are considered automotive-grade connector solutions.
Amphenol offers a variety of wire-to-board systems designed to be highly vibration resistant, including a primary latch and terminal and connector position assurance along with a range of thicknesses, operating temperatures, waterproof capabilities and positions. Their FPC-to-board systems are USCAR vibration and shock compatible and offer easier assembly, less weight and are more cost effective compared to discrete wire solutions.
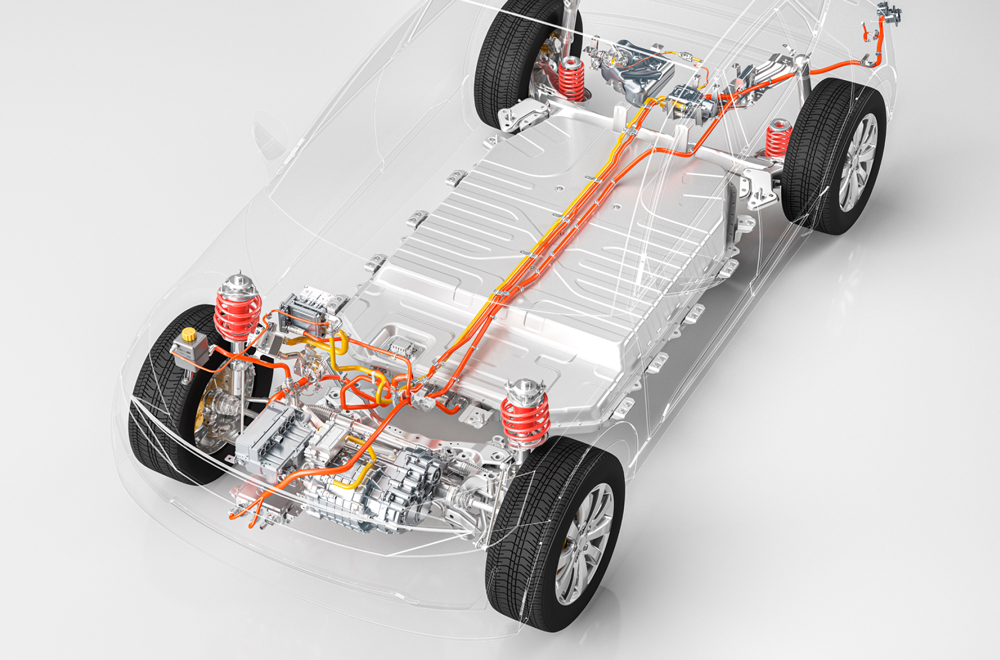
Temperature monitoring
The ability to monitor and regulate the temperature of lithium ion batteries is critical for their operation. Cells perform best at a temperature range of about 10°C to 60°C, but the process involved in charging and discharging lithium ion batteries generates heat. If the temperature is too low when charging, dendrites can grow and cause permanent damage to the cells, while higher temperatures enable more rapid charging but can sacrifice cell life. Thermal management control is needed to prolong the life of the battery pack, especially in large arrays that might have up to 4,000 cells in a system.
Sensors are essential to managing battery system temperatures. Components such as thermocouples, resistance temperature devices and negative temperature coefficient thermistors can directly measure temperatures, while infrared sensing is a non-contact option. Most industrial and transportation controls use the highly-sensitive thermistor temperature sensing technology. Thermistor sensors can be surface mount or lead wire designed and placed on flex circuits, epoxy potted, overmolded or place in probe geometries.
In this electrically noisy environment of that includes inverters and transformers, sensors need to withstand electromagnetic noise, which can induce current on sensor wires. With the increasing complexity of electric systems and the density of electronic components in modern vehicles, conventional negative temperature coefficient thermistors are vulnerable to stray electromagnetic interference, which can cause self-heating. Traditional solutions such as using a twisted pair wire assembly can become costly, so Amphenol has implemented a filter capacitor technology integrated with the thermistor that uses a radio frequency decoupling function, which provides protection against electromagnetic interference at the component level.
When it comes to coolant and refrigerant temperature sensors, non-contact infrared temperature sensing is often used. This solution works for high voltage applications such as charger-to-wire and interconnects and within enclosures. Amphenol’s infrared-based thermal monitoring solution meets IEC 60664 clearance requirements and boasts a 20-millisecond time response.
The small-scale residential storage market, as well as large-scale “behind the meter” storage markets, are growing rapidly. At the residential level, passive cooling, convection cooling and liquid cooling methods are used, requiring temperature sensor feedback on cell surfaces as well as the monitoring of coolant temperature. For large-scale electric stationary storage systems, forced air convection cooling and liquid cooling are used. This requires more robust monitoring, including the temperatures of the enclosure and battery busbar, as well as humidity, water intrusion/coolant breach, non-contact temperature monitoring of high voltage components, and thermal runaway detection. Ambient air temperature and rain sensors may be needed as well for applications such as weather stations
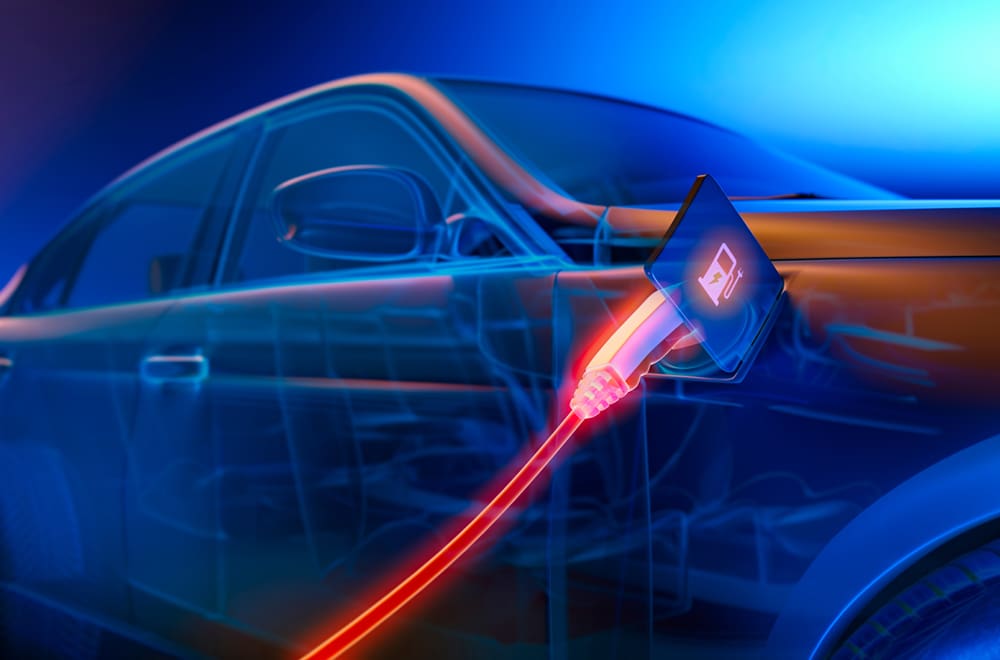
Liquid and thermal runaway monitoring and detection
While temperature monitoring is an important element to safe and efficient lithium ion battery management, there are other elements that require early detection. Coolant leakage and water intrusion can cause significant issues, including accelerated corrosion and thermal runaway. Recent recalls at GM and BYD due to liquid intrusion highlight the importance of early detection of any water within the system.
Amphenol’s coolant breach/water intrusion detection sensor is useful for both coolant breach and water intrusion detection and can identify as little as 3mm of conductive liquid in the battery enclosure. The sensor is resistant to condensing events and is often deployed in traction battery packs, stationary storage systems and chargers.
Thermal runaway in lithium ion batteries is another challenge that can be mitigated with early detection. Although internal combustion engine vehicle fires occur once every three minutes in the United States and electric vehicles have a 90 percent lower probability of experiencing a fire incident than ICE vehicles, battery malfunctions still make the headlines—and offer unique challenges to first responders.
In electric vehicles, battery packs are often difficult to access, and thermal runaway temperatures can exceed 1,000°C while emitting hazardous and flammable gases that increase the risk for explosion. Gases, particulates and water vapor from the battery, combined with high voltage systems, can increase the risk of arc discharge. Lithium ion battery fires are long duration events as the batteries provide their own oxygen to support combustion and damaged cells can cause reignition. It can be difficult to assess the state of the battery cell or pack and determine the end of the event, and fighting these fires requires training, new processes and new tools.
Identifying a potential thermal runaway requires an intelligent sensor capable of quickly detecting even a single cell venting within a large array. Amphenol’s Robust Early Detection of Thermal Runaway (REDTR) solution utilizes physics-based gas detection of initial cell venting using hydrogen and carbon dioxide sensors and is capable of operating independently of the BMS to allow the BMS to “sleep easy” while REDTR maintains a continuous watch over every cell in the pack. With a small package size and a design life of more than 20 years, REDTR will maintain vigilance over battery safety from production to recycling.
Amphenol offers a variety of temperature sensors, pressure sensors, current sensors, position and speed sensors, along with a variety of custom devices for batteries, thermal management systems, motors and fuel cell technologies, making them a one-stop shop for sensors. Amphenol’s portfolio of sensors that enable the early detection of thermal runaway as well as coolant breaching water intrusion detection, EMC-immune temperature sensors, noncontact high-voltage component temperature sensors and thermal management applications. Amphenol’s deep understanding of battery behavior also makes them one of the world’s largest suppliers of cell connection systems (CCS) for battery systems, helping sense, communicate and move energy for a long, durable battery life.
Sponsored by TTI and Amphenol
[ad_2]
Source link