[ad_1]

Sponsored by Arkema
In the near future, the number of electric vehicles on roads across the globe will increase dramatically. This growth is being driven by new regulations, increased public demand for greener transportation and, ultimately, the goal of reducing greenhouse gas emissions. In fact, according to the UN Climate Change Conference, the global automotive fleet will be composed of more than 30% EVs by 2030.
Many challenges remain in EV design in order to drive more mainstream adoption. A key area of focus for the industry is on the battery and charging systems used in these vehicles. Despite all the progress made on battery design and battery energy density, there are still design challenges that could slow the mass adoption of EVs. Two of the key challenges are battery charge times and overall safety of the battery. One technology that could help resolve those challenges is liquid immersion cooing of batteries. Liquid immersion cooling is an extremely promising technology for the thermal management of batteries. In liquid immersion cooling, the battery cells are completely immersed in a dielectric fluid, providing better thermal performance than the current thermal management solutions. In addition, immersion cooling could enhance the safety of the battery.
There are many dielectric fluids that can be selected from for use in immersion cooling. Options range from dielectric oils to pure fluorinated fluids. Recent developments are showing that some non-fluorinated dielectric oils can achieve even better performance with the addition of a fluorinated booster. This booster enhances the dielectric properties of the oil, which provides a positive impact throughout the entire system.
Fluorinated boosters for dielectric oils were introduced by Arkema in 2020 to support the adoption of Immersion cooling technology. Arkema’s booster is a fluorinated fluid with a very low global warming potential. It is non-flammable and non-toxic. The booster has excellent miscibility with most dielectric oils, and is commercially available at industrial scale.
Fluorinated boosters combined with a dielectric oil help reduce the viscosity and suppress the existing flashpoint of the dielectric oil. The addition of the booster does not have any negative impact on oil or component aging and does not adversely impact thermal performance of the pure dielectric oils.
When mixed at 10% weight in a dielectric oil, the viscosity of the blend is half the viscosity of the pure dielectric oil, at both ambient temperatures and low ambient temperatures (-20°C). This trend has been verified through testing using a variety of different dielectric oils.
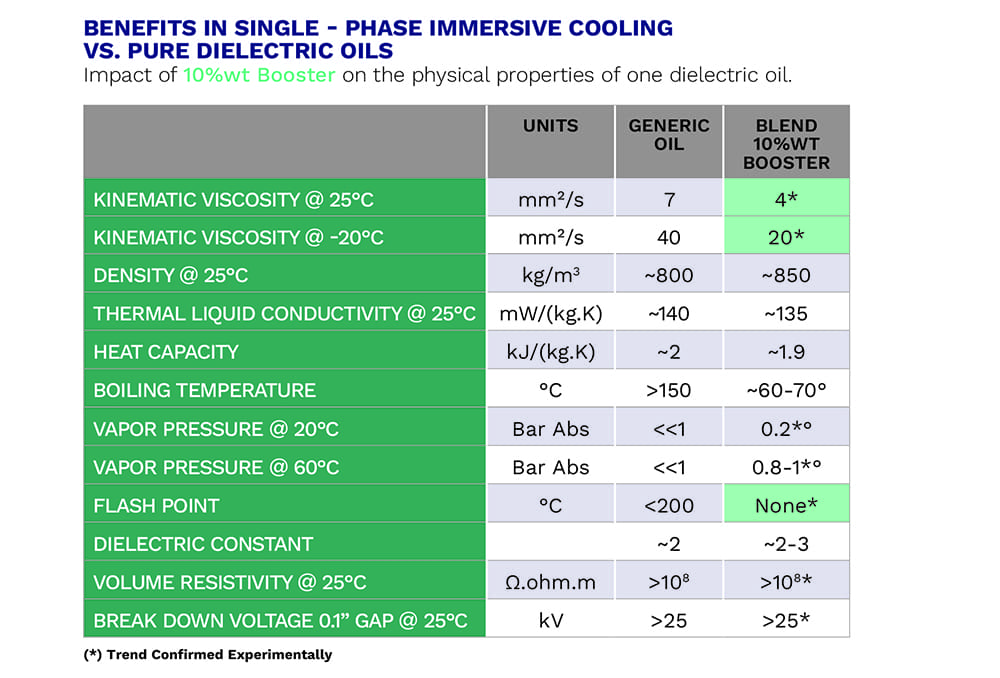
Thermal performance of the fluorinated booster and dielectric oil blend was evaluated at the module level in a battery system designed by an original equipment manufacturer (OEM). Testing was done for more than 500 cycles with a charging speed up to 4C, which constitutes a 15 minute charge time. In this study, a blend of 10% booster/90% dielectric oil. It was tested along with pure dielectric oils[Figure 2]. The results showed that the addition of the booster did not negatively impact the thermal performance of the dielectric oil. Both the aging of the cells and the thermal performance of the module were similar with or without the fluorinated booster.
Many lower viscosity dielectric oils exhibit a flashpoint lower than 150°C .The addition of the fluorinated booster suppresses this flashpoint of dielectric oils and lowers the viscosity of the fluid. This allows the use of a wider range of dielectric oil possibilities without having to pick between having an increased flashpoint temperature or a lower viscosity, which typically increase proportionally in pure dielectric oils.
Improved Safety
One of the most important aspects related to safety of battery electric vehicles, is the prevention of thermal runaway in the battery. Thermal runaway occurs when one battery cell reaches temperatures that cause a chemical reaction within the cell. Once the chemical reaction in a cell begins, it can quickly spread to other cells within the battery, starting a thermal runaway event. Immersion cooling can potentially help prevent thermal runaway events from occurring. Dielectric fluorinated fluids and fluorinated boosters could be key in enhancing prevention of thermal runaway events. At the cell level of an immersion cooled battery, the absence of thermal runaway propagation was validated through nail penetration abuse tests.
Tests were performed with both pure dielectric fluorinated fluid and a blend consisting of 90% dielectric oil and 10% fluorinated booster . The test results showed no thermal runaway propagation from the damaged cell to the other cells within the pack. Adding high percentages of fluorinated booster to the dielectric fluid blend reduces the impact of thermal runaway propagation to adjacent cells even further. The gases exhausted during testing were analyzed and no evidence of degradation of the booster was found.
Similar tests were performed at module level. The module was designed by an automotive OEM and worked in a full-immersion cooling mode with 1.9 L of a blend consisting of 90% dielectric oil and 10% fluorinated booster. It was a 21.9 V module made of 62.5 Ah NMC prismatic cells, with a volume of 13.5 L. The energy density to module volume was 200 Wh/L and 1 450 Wh/L to fluid volume.
Abuse tests were performed without any fluid recirculation to simulate the worse case scenario. The blend containing the fluorinated booster was compared to the pure dielectric oil. Figure 3 shows the significant impact the booster had on the exhaust gas temperature after ignition. Both at the outlet of the module and 1 meter further, maximum gas temperature was at least 100°C lower.
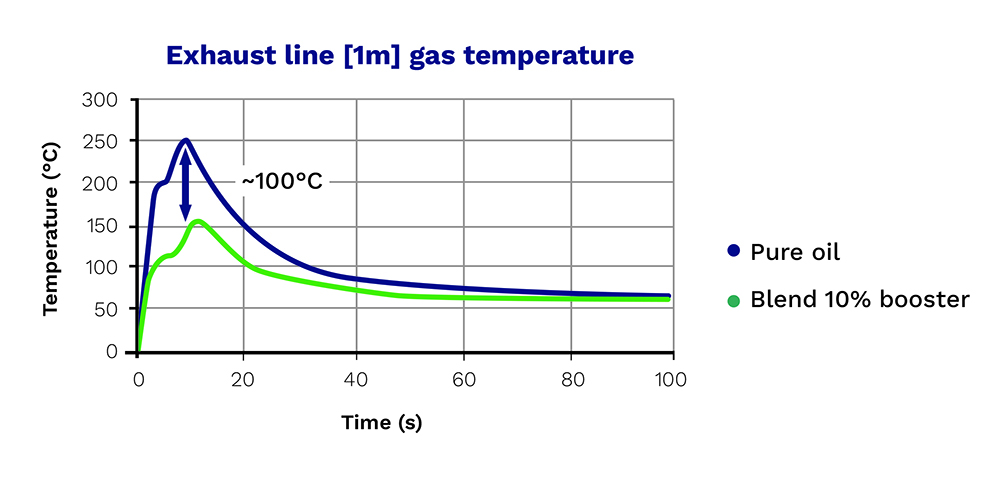
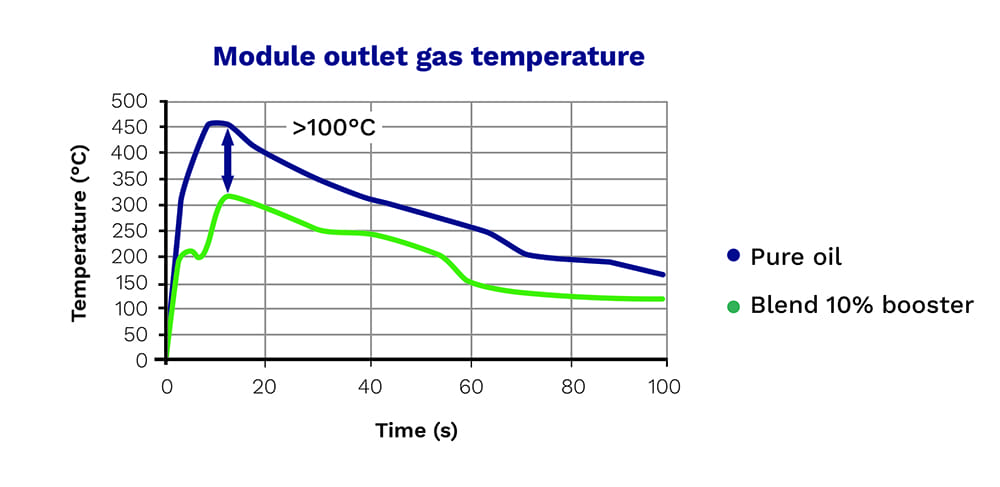
Liquid Immersion Cooling Can Offer Design Flexibility
The addition of a fluorinated booster at a 10% level to a dielectric oil reduces the viscosity by 50% on average compared to the pure dielectric oil. This reduced viscosity leads to lower pressure drops measured in the system, a difference of up to 30% at 0°C and 45°C. This viscosity reduction results in the ability to use smaller pumps, smaller cooling lines and faster filling times. The use of the booster puts fewer design constraints on engineers and could be a conduit for cost savings at the OEM.
Material Compatibility
Material compatibility assessments were completed to ensure that the addition of the booster would not result in any unforeseen issues with the choice of materials of construction . Many different polymer families were tested, comparing the pure booster, a pure PAO oil, a pure POE oil and booster oil blends. Results showed that the booster has very limited impact on material compatibility and the results were mostly the same as were seen with pure oil or blends, except for FKM (fluoroelastomer) which demonstrated a degraded compatibility.
CONCLUSION
Immersion cooling could hold the key to enhanced battery performance which would allow faster charge rates, extended battery life, and enhanced safety performance of electric vehicles. High performing dielectric fluids will be essential in bringing immersion cooled batteries to the mainstream. Since the research into fluorinated boosters for dielectric fluids has begun, significant progress has been made towards demonstrating how they can be used to enhance the performance and safety of dielectric oils. Testing through multiple engineering, component, and OEM partners has shown reduced oil flashpoints and improved thermal runaway propagation prevention on both cellular and modular levels of the battery. This improved performance could greatly enhance the safety of batteries in many electric vehicles across the globe. In addition, fluorinated boosters help reduce the viscosity of dielectric oils that often have very high viscosity at low ambient temperatures. Reduced viscosity allows greater design flexibility to automotive engineers by reducing fill times in the manufacturing process, pumping power, line sizes, and overall component costs. Immersion cooling using dielectric oil/fluorinated booster blends offers many advantages over current battery thermal management methods. Continued collaboration with component and OEM partners will further prove this technology and contribute to further mainstream adoption of electric vehicles across the globe.
[ad_2]
Source link