[ad_1]
In recent years, high power electronics have become one of the fastest growing market segments of the semiconductor industry. Power electronic modules used therein are typically operating at high voltage and high current density and must cope with high temperatures and harsh conditions. The demand for higher efficiency of electrical drive systems in e-mobility, meaning longer travel distance or higher speed per battery loading, requires high power density packaging solutions, perfectly matched material combinations providing high temperature stability and maximum reliability of drivetrain inverters in electric vehicles.
Increased power density and operating temperature of a power module require more efficient and highly reliable interconnections to fulfill the demands.
Join this free webinar at our Fall Virtual Conference (October 17-20, 2022), presented by Heraeus Electronics, to learn about the development of the Die Top System to enable copper wires or ribbons be placed on top of the die. We will discuss:
- The combination of the Die Top System with power Cu wire/ribbon can maximize the power density and power cycling reliability/lifetime of a power module.
- Matched pre-applied sinter pastes and the functional surface of the Si3N4 AMB substrate provide robust and simplified die assembly results in improved die shear strength and reliability.
- Pre-sintered metal ceramic substrates are the alternative for module manufacturers who look for simplified production processes and prefer to use pre-applied sinter material instead of printing paste.
Other sessions at our Fall Virtual Conference include:
CHARX DC Power Electronics For EV Charging Infrastructure
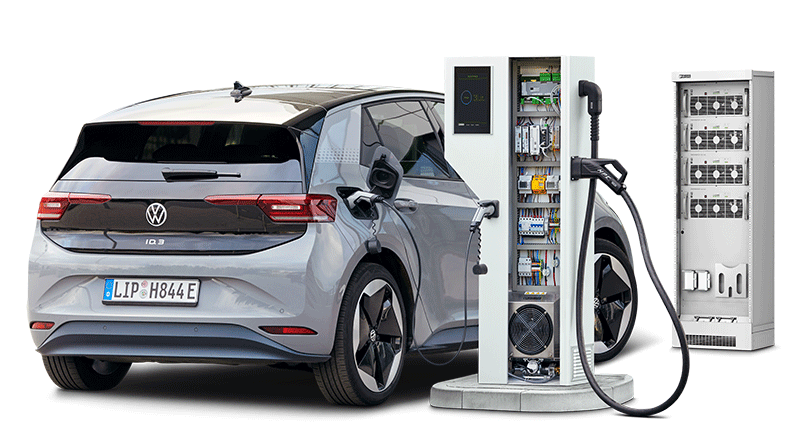
The EV charging market is developing quickly with system design and government funding.
This session will cover the growing markets and applications for the CHARX power components recently introduced by Phoenix Contact. Join us to learn the features of the CHARX products that will your customers power up their EV charging applications.
EV Lubes: The Latest In Driveline E-Fluid Technology
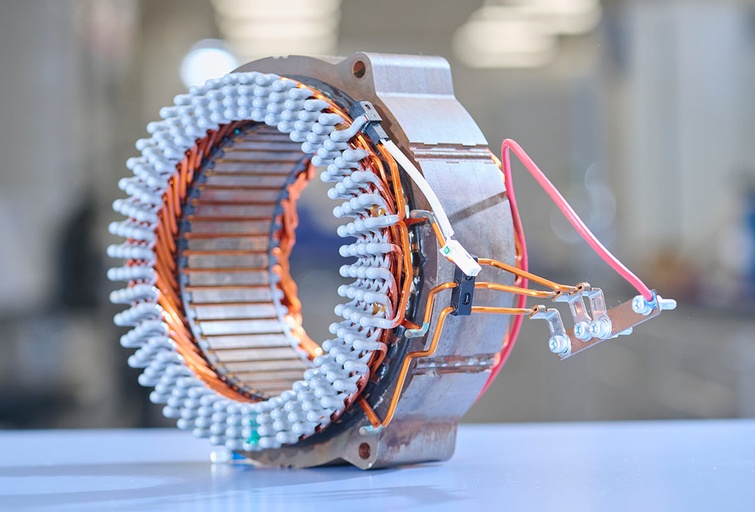
New driveline e-fluids, designed to enable the latest electrified powertrains to perform at their very best, are entering the market.
Many earlier electric vehicle powertrains were developed using automatic transmission fluids (ATF). Not optimised for EVs, increasingly these are being superseded by the latest generation of lubricant fluid technology, termed driveline “e-fluids”. e-Fluids are optimised for automotive electrified hardware types, such as the latest generation of e-axles, and cool and protect such devices much more effectively. With lubricants now increasingly expected to be in direct contact with powered motor windings and exposed electrical components, characteristics such as preventing copper corrosion and raised fluid electrical resistivity are of increased importance.
Motor efficiency increases with reduced fluid churning losses and suitable cooling. It can be further improved through the use of optimised viscosity fluids which provide thermal management. Ensuring suitable wear performance as required by the hardware engineers is of vital importance to protect the gears and bearings, and is another benefit provided by the e-fluids.
This session will be of interest to engineers seeking an understanding of the fundamental principles behind e-fluid design. In addition, the latest fluid testing methods to address some of the hardware challenges, resolved by the fluid, will be described with the aim of enabling the engineer to make the best fluid choice for their latest hardware designs.
Register here to learn more—it’s free!
Using Materials Science & Precision Converting to Solve the Thermal Runaway Problem: A Panel Discussion
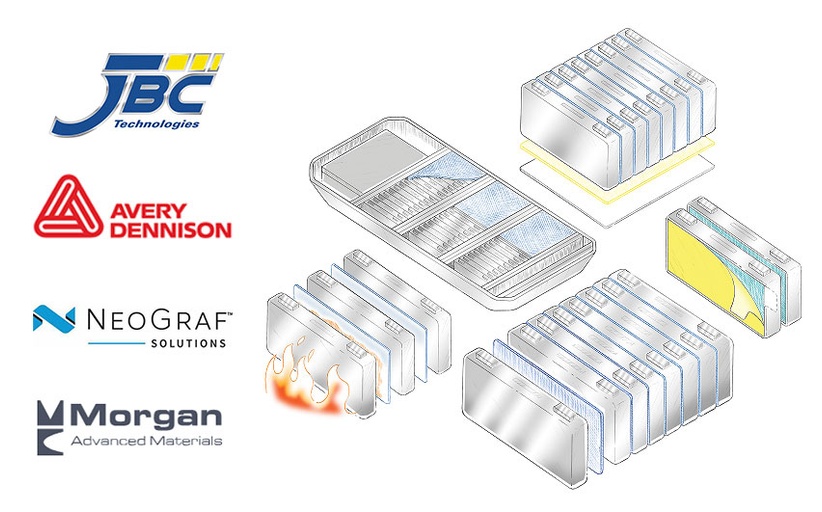
Drivers of electric vehicles want to be able to achieve a full charge as quickly as possible. They also want long-lasting batteries. But fast charge/discharge cycles generate excess heat that is detrimental to the life of the battery. Product designers need a way to pull the heat out as fast as it comes in. They also need a way to protect cells from damage as the cells expand and contract.
So how do you protect cells from excess heat generated during the fast charge and discharge cycles required for high performance day-to-day operations. And what do you do with all that thermal energy if something goes wrong?
In this session, JBC Technologies has assembled a panel of experts to help provide answers to these questions and more, covering:
- Where and how custom converted specialty materials can be used within the EV Battery Pack to improve the user experience and enhance vehicle safety
- High-performance materials that can be used spread, shield, and isolate heat to help you achieve these objectives
- Why incorporating multiple materials into a single part is key to reduce the vehicle weight, and cost, while increasing battery range
- The flexible materials converting technologies that make it possible to fabricate multi-functional materials
Register here to learn more—it’s free!
Virtual Twin For Battery Engineering
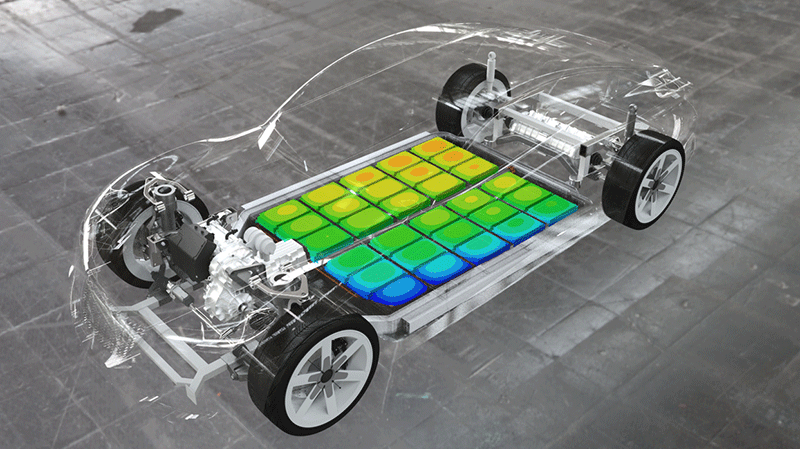
With the rise of Battery Powered Electric Vehicle, our world is becoming more and more dependent on batteries especially in Transportation & Mobility and High Tech industries. These disruptive changes are driven by regulations and consumers demands (Range, cost, sustainability, etc.).
The complete value chain from material suppliers to Battery makers to Automotive/High Tech OEMs are facing challenges associated with designing & integrating high energy & density battery systems. They need to find a way to optimize battery performances over a wide range of operating conditions while preventing safety issues and reducing battery cost.
Batteries are highly complex systems, requiring advanced engineering methods at all levels: from chemistry to cell engineering, to module and pack engineering, and finally integration into full vehicles.
In this presentation, you will learn about end-to-end solution provided by Dassault Systemes, which captures all of these scales. We offer technologies ranging from electro-chemistry modeling capabilities to optimally design battery materials for aging; 1D/system simulation for cells, modules, and packs; as well as full 3D representation of the battery cell, module and pack integrated into full vehicle models to be simulated for realistic test conditions.
Register here to learn more—it’s free!
See the full session list for the Fall Virtual Conference on EV Engineering here.
Broadcast live October 17 – 20, 2022, the conference content will span the EV engineering supply chain and ecosystem, including motor and power electronics design and manufacturing, cell development, battery systems, testing, powertrains, thermal management, circuit protection, wire and cable, EMI/EMC and more.

[ad_2]
Source link