[ad_1]
Bikerumor may earn a small commission from affiliate links in this article. Learn More
Nestled in the Mississippi river valley in Southwest Wisconsin sits Blue Steel Bikes. BSB is a one-man frame builder specializing in steel and titanium bicycle frames. Paul Reardon has been in business and welding frames since 2010, starting off with lugged and fillet brazed steel road and mountain bike frames.
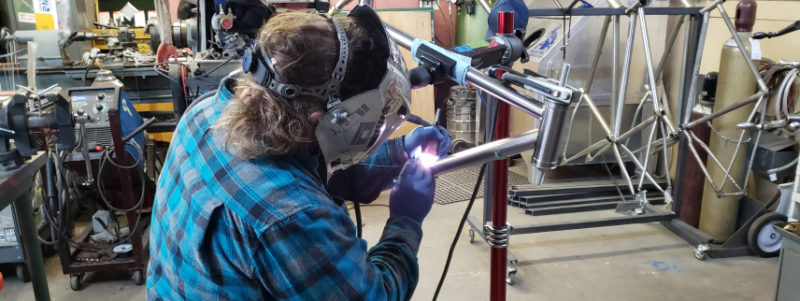
After enrolling in the United Bicycle Institutes titanium program back in 2016, titanium frames are now 90% of the business these days.
Their location sits at quite a bit of elevation in the driftless region of South/West Wisconsin. Paul says, “with Iowa and Mississippi right across the river, we have some of the best gravel around. As you can imagine we primarily build gravel, and road plus bikes due to our location”.
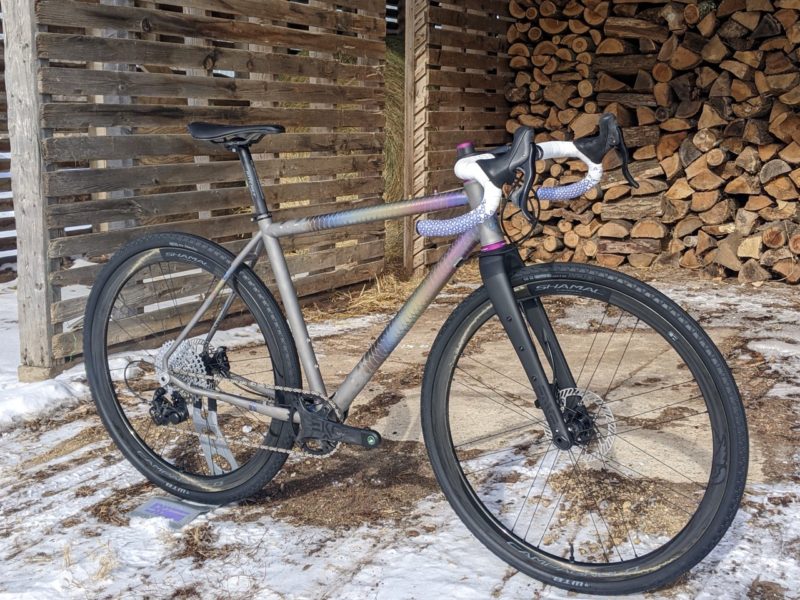
BSB does all of its frame design, machining, welding, and anodizing in-house. The shop is a small 2000 square foot space with everything they need to build your frame.
They don’t do any production frames, only custom frames built one at a time for each client.
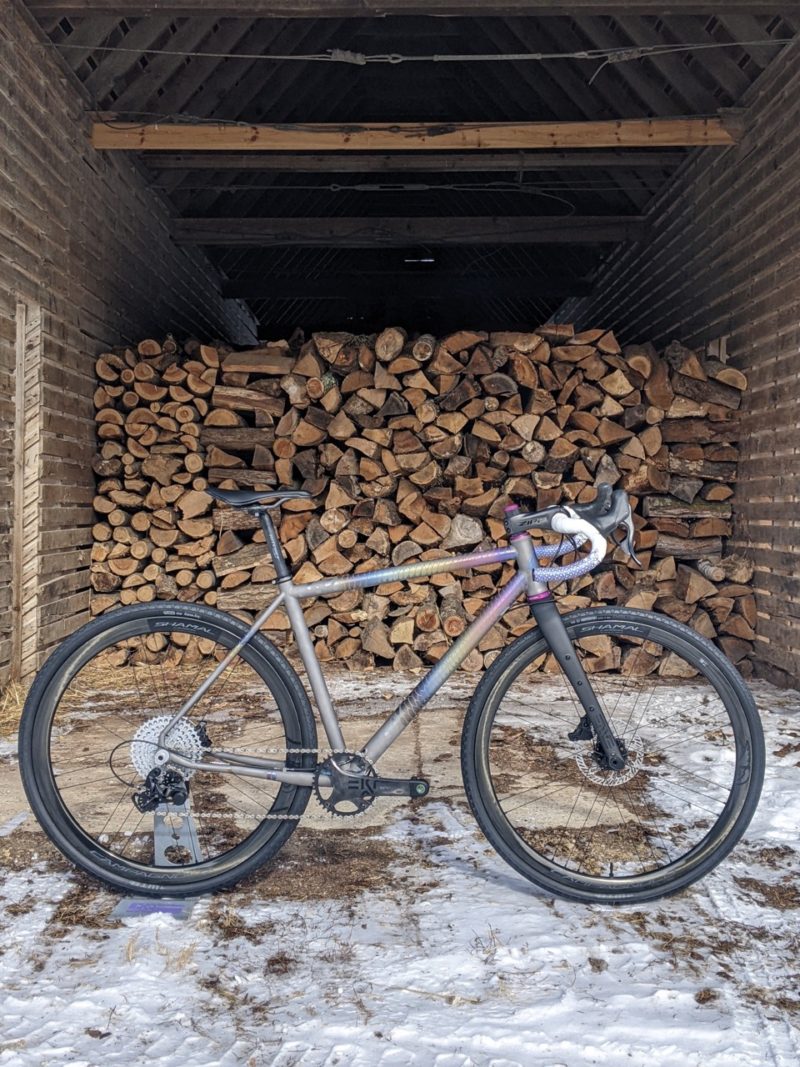
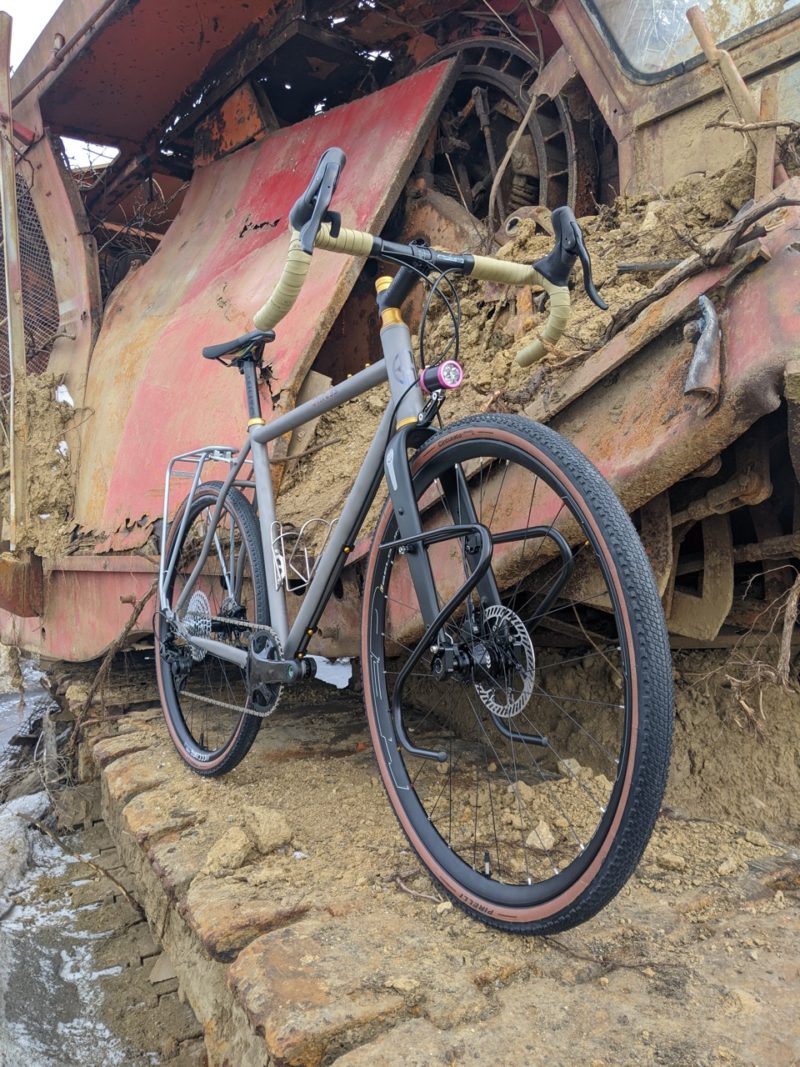
The Order Process
Step One: Let’s Get the Ball Rolling
A simple email or phone call will get things started. A preliminary conversation about what you are looking for is the first step. I always encourage clients to schedule a time to come by the shop and discuss things in person. We are starting a journey together, so let’s get to know each other. We can discuss your dream bike, and go over our process.
Step Two: Make a Down Payment
We require 50℅ down to reserve your place in the queue. This allows us to order materials for your build. Balance s due upon delivery. Down payments are non-refundable.
Step Three: The Fitting
With every custom frame build, we included a professional fitting. We work with Dr. Deb Slota at Bike and Body in Milwaukee. Deb is a fantastic fitter, and can address the needs of your body, and generate precise fit numbers.
Step Four: Design
Designing your frame will be a mix of several factors. What is the intended use of the bike? Ride and handling qualities are all combined with your fit numbers. This is a process that can take a bit of time to nail down exactly what you want. We can add things like rack and fender mounts to S and S Couplers here. The process will include a cad drawing that we will discuss, and adjust. Once a final draft is agreed upon, we make a life-size drawing on the table.
Step Five: Production
This is where we machine the tubing and do fit up in the fixture. Once the tubes are cleaned and prepped it is time to join the tubes (welding, brazing, or both). The frame will be assembled in the fixture and aligned post-weld on our alignment table.
Step Six: Finish Work
We offer a variety of finish options for titanium, like etching, in-house anodizing, high polish, or matte finish, we want to make your bike unique to you. We offer powder coating for our frames too. If you prefer wet paint, we have a few painters we work with but are not equipped to do this in our shop.
*All frames will be chased and faced in preparation for final assembly.
Step Seven: Assembly
We work with all major component manufacturers and can equip your bike with any part you fancy. Custom wheels to bar tape, all the fixings are available. Give us a call, and we can start planning your future today. One bike at a time, just for you. We look forward to working with you.
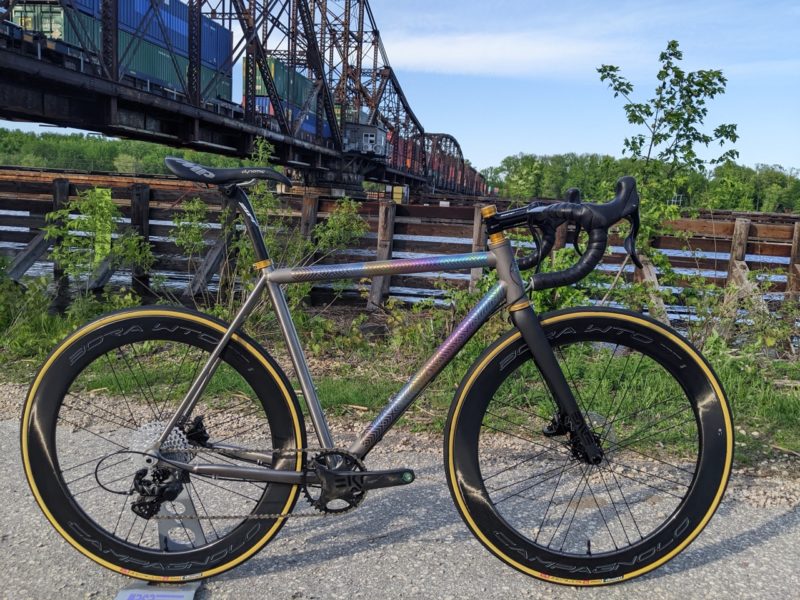
If you’d like to find out more or ask Paul any questions about your possible next bike build… Call: (970)-470-6668 or send an email to [email protected]
[ad_2]
Source link